Zhongjin Matai's Choice of VOCs End Treatment Technology
As a responsible and responsible enterprise, Zhongjin Matai started to control the VOCs emissions of the factory as early as 2008. In order to achieve VOCs emission reduction, CICC Matai mainly starts from the two aspects of end control and source control, and treats both the symptoms and the symptoms.
Refers to the end of the treatment is mainly installed exhaust gas treatment apparatus, the exhaust gas printing machine, coating machine, and the multifunction peripheral discharge is recycled. In packaging and printing production, due to the low exhaust air volume, high concentration, and single VOCs emission component produced by the dry composite process, generally activated carbon fiber adsorption + low pressure steam regeneration recovery technology, granular activated carbon adsorption + nitrogen protection regeneration recovery technology, Granular activated carbon adsorption + low-pressure steam regeneration recovery technology, the recovered solvent (mainly ethyl acetate) is purified and reused.
The exhaust gas concentration generated by the printing process is low, and the VOCs emission components are more complicated. Generally, adsorption recovery technology (activated carbon fiber adsorption + low pressure steam regeneration recovery technology, granular activated carbon adsorption + nitrogen protection regeneration recovery technology or granular activated carbon adsorption + low pressure water vapor) Regeneration recovery technology), adsorption concentration + catalytic combustion technology.
In accordance with the three principles of " reduction, reuse, and recycling " in line with the circular economy, Zhongjin Matai purchased 2 sets of solvent recovery devices and 2 sets of regenerative exhaust gas treatment devices (referred to as "RTO") using the condensation recovery process Installed in SP ( flexible packaging ) factory and PTP (blister packaging) factory respectively.
Condensation recovery process route and cost analysis
01 craft route
(1) The first adsorption stage
The organic waste gas discharged from the printing and compounding process is pressurized by a high-pressure fan, and the impurities in the waste gas are filtered through a filter, and then the temperature of the waste gas is reduced to normal temperature through a cooler, and then distributed into multiple first-level adsorbers through a wind collector and finally absorbed Make the clean air after adsorption reach the standard. Real-time monitoring of exhaust gas emissions, when a certain adsorber discharge exceeds the standard, it will be switched off.
(2) Primary desorption and secondary adsorption stages
Before desorption, nitrogen gas needs to be replaced in the system. The high-pressure fan in the system is blown and circulated. After being heated to 170 ° C through a high-temperature heat exchanger, it enters the first-level desorber. Device adsorption, so far all the primary desorption and secondary adsorption have been completed.
(3) Secondary desorption stage
The high-pressure blower in the system circulates through a high-temperature heat exchanger to 170 ° C and enters the secondary desorber. After decomposing the adsorbed organic solvent, it enters the condenser to cool down, condensate and recover into a liquid state.
(4) Solvent distillation
The original recovered solvent enters the solvent post-processing equipment, and the organic solvent recovered raw liquid is deacidified, dehydrated, decolorized, deodorized, separated and purified through the rectification equipment, and then re-entered into the workshop as a raw material for production.
02 Cost Analysis
The unit investment cost is 1.5 million yuan (3t / day recovery capacity) for every 10,000 air volumes processed. The average cost of recovering 1t of solvent is about 1086 yuan (as shown in Table 1). The average cost of purifying 1t of solvent is about 682 yuan (as shown in Table 2), the value of the solvent after purification (including tax) is about 5,000 yuan / t, and the recovery energy utilization efficiency reaches 64%. The main technical indexes of the process control effect of the condensation recovery method are shown in Table 3.
Table 1 Cost of recovering 1t of solvent
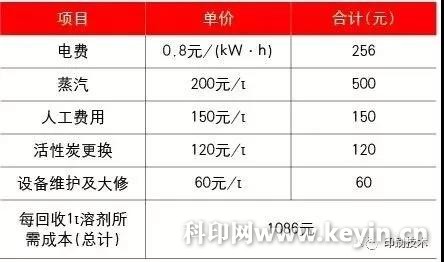
Table 2 The cost of purifying 1t of solvent
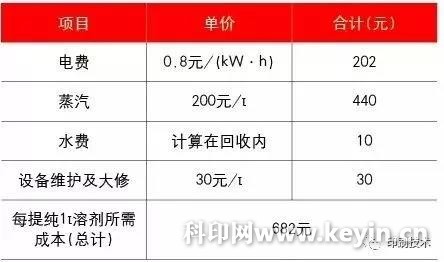
Table 3 The main technical indicators of the process control effect of the condensation recovery method
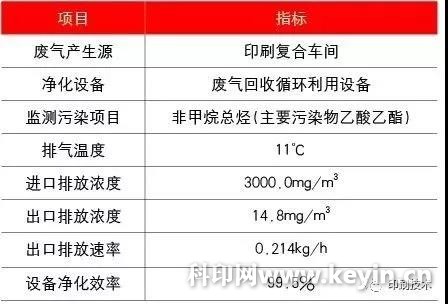
Transfer Patient Lift,Bariatric Patient Lift,Patient Lifting Device,Battery Powered Patient Lift
Jiangmen Jia Mei Medical Products Co.,Ltd. , https://www.jmmedicalsupplier.com